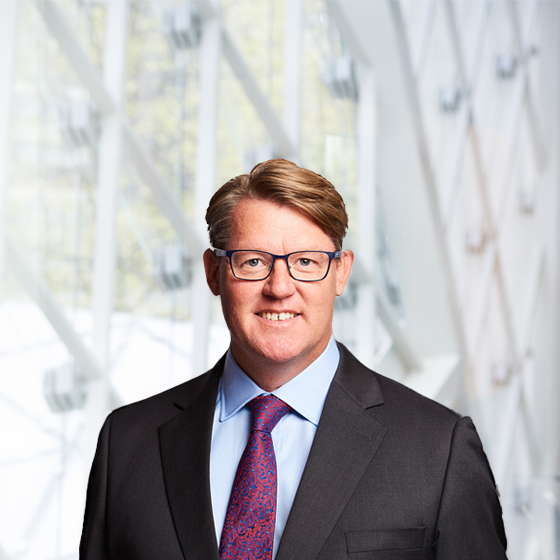
Richard Austin
Manufacturing remains one of the key industries for the UK - in its various guises the UK manufacturing industry employs almost three million people, contributes approximately half of UK exports, two thirds of business research and development - and the UK is currently the ninth largest manufacturing location in the world.
There are plenty of opportunities for British manufacturers to gain a competitive edge, as individual organisations and as a collective industry. The strength of UK manufacturing remains excellent service, supported by extensive Research and Development (R&D) and innovation, as well as making use of new and emerging technologies.
The movement towards more automation, digitisation and new materials ("Industries 4.0") is expected to have significant opportunities and challenges; UK manufacturers will need to change and invest to keep pace with global competitors. The pace of change over the next five to ten years will be rapid, requiring new thinking as to how best to use the different techniques that will be developed through Industry 4.0. This is likely to have short term (pressures to automate, digitise through the supply chain, reduce costs) and long term (education, skills, training) implications.
Manufacturing is a priority industry for BDO, and this focus enables us to tailor the wide range of services we offer and apply our specialist skills and knowledge to help you achieve your objectives.
We provide real solutions to industry issues, using our capabilities in everything from sector-specific accountancy, tax and business advice to patent box and R&D claims and M&A opportunities to help our clients grow in the UK and overseas. We also provide manufacturing businesses and organisations with robust, independent audits.
We understand the key issues affecting UK manufacturers as an industry, but we also focus on some specific sub-sectors to further tailor our knowledge and our services. These include:
We are proud to work closely work key industry bodies such as Make UK and SMMT. These organisations work closely with manufacturing businesses and have developed a strong reputation as supporters of the industry and expert commentators on a wide range of issues.